Peter Bassett, President of EPS, Kevin Dunbar, Corporate Energy Group Supervisor of Stellantis and John Nicol, Program Director, Energy Efficiency Services of Leidos wrote a paper titled Stellantis drives Operational Savings During COVID for the ACEEE (American Council for an Energy Efficient Economy) Industrial Summer Study held virtually in 2021. Peter Bassett presented the paper at the Summer Study via web.
Stellantis drives Operational Savings During COVID
Peter Bassett, President, Energy Performance Services (EPS)
Kevin Dunbar, Corporate Energy Group Supervisor, Stellantis
John Nicol, Program Director, Energy Efficiency Services, Leidos
ABSTRACT
DTE Energy introduced a new Strategic Energy Management program (“SEM Program”) to the large industrial sector in Michigan in late 2019, which Fiat Chrysler America (“FCA” or “Stellantis”) signed up five (5) manufacturing plants to participate in. The initial SEM Program runs for a 24-month period and focuses on delivering “operational” energy savings to help meet DTE Energy reduction targets as well as Stellantis energy and carbon reduction goals. Leidos is the prime contractor for management of the SEM Program and has sub-contracted Energy Performance Services (“EPS”) to work directly with the participating sites. Within a few months of starting the first two Stellantis facilities in the SEM Program, COVID-19 hit with full force and impacted the Stellantis facilities in a significant way causing plants to shut down and shift into an “idle” mode. The joint SEM team however innovated an approach to drive reductions in “idle” energy through the application of an innovative “operational control” table (shown in Table 1) that the facility personnel were instrumental in using to control significant energy consuming systems via digital interfaces to deliver substantial operational energy improvements despite the impacts of COVID-19. This approach has leveraged an Energy Team, the manufacturing workforce, enhanced energy management information and employee engagement outreach to drive control over energy from the factory floor. Stellantis was able to transfer some of the approaches developed in the SEM Program during COVID-19 to other facilities across North America and Stellantis achieved a record year for energy performance improvement despite the challenges of COVID-19.
Background of Stellantis in Energy Management
At Stellantis, in North America, energy in the Manufacturing facilities is managed by the Corporate Energy Group (the “CEG”). The CEG is responsible for tracking energy usage across North American Manufacturing locations in addition to managing the energy projects that occur at those facilities. There are over 26 Manufacturing facilities in North America consisting of
Assembly, Stamping, Transmission, Engine, Casting, and Machining type facilities located in the United States, Canada, and Mexico. The CEG is located inside the Manufacturing Operations, in particular, the Facilities Group. This allows for great interaction with the subject matter experts in the different centers (General Assembly, Body in Weld, Paint, Facilities) and the ability to drive energy change within the existing standards or specifications. Each Manufacturing facility has an Energy Champion that is responsible for driving energy consumption reduction and is the key contact of the CEG to communicate all items related to Energy. The CEG is aligned with Senior Management and has upper-level support to align and drive energy reductions.
In 2018, an Energy Strategy was developed which consists of four main principles: Financial, Technical, Communication, and Knowledge. This Energy Strategy is used currently and was approved by Senior Management. All actions of the CEG exist around these main
principles and it allows for maximum energy savings. Let’s take a look at the four principles in detail.
Financial
The CEG monitors and tracks financial results – after all, the ultimate goal is to reduce consumption, which typically reduces the overall spend on utilities. In the Financial world the CEG looks at driving energy cost down and receiving benefits (rebates/incentives) where possible. Items that are core to this principle include: Cost Savings Initiatives, Monitoring Capital and Infrastructure projects for energy efficiency/savings, Maximizing Energy Efficiency rebates, Participating in Demand Response programs, Monitoring and increasing non-production curtailment, and tracking Energy Key Performance Indicators (“KPI’s”) and budgets. As with most companies, the “bottom line” is crucial. The CEG strives to reduce cost year over year and maximize opportunities to receive money back for the company. This is one of the factors which drove the organization to join the SEM pilot with DTE Energy. Maximizing the operational savings to provide incentives and savings is a cornerstone to our founding principles. As with any financial data, this information is tracked on a weekly/monthly basis to ensure that we hit our goals and provide value for the organization.
Technical
The CEG is responsible for the technical operations of energy efficiency. The CEG is made up of five (5) total individuals, with highly skilled energy professionals which manage and assist the Manufacturing facilities with energy know-how. From the Technical side, the CEG is involved in the following: Energy Health Assessments, Energy Treasure Hunts, Cross Energy Meetings, Best Practice sharing, and management of the ISO 50001 energy management system. All the Manufacturing facilities within North American are ISO 50001 certified which allows all facilities to manage energy in a very systematic/standard manner. The CEG originated the Energy Treasure Hunts within Stellantis. Since the first Energy Treasure Hunt in 2018, the group has managed to complete all facilities and has found millions of dollars of energy savings opportunities, which include no cost, low cost, and capital improvements. Another very important aspect of the CEG activities is the Best Practices sharing. On a regular basis, the CEG hosts a meeting with all Energy Champions at each facility, at that meeting Best Practices and successful projects are shared with all facilities to maximize the success of other projects. It is during these meetings that Stellantis can take lessons learned from the SEM Program and share it with the other facilities to become more efficient. One example of sharing best practices was the use of the Operational Table to drive curtailment during non-production periods. This is a very simple table that highlights what key energy systems should be running and who is responsible for operation of that equipment.
Communication
Communication is core to the success of CEG. With many different locations and individuals to reach out to, it’s important that the communication plan is in place and able to reach all facilities effectively. In our communication plan, we include: the regular interactions with the Manufacturing facilities Energy Champions, the Management communications, the Global communications/harmonization, ability to provide awareness and recognition for energy
achievements, and benchmarking both internally/externally. As mentioned above, the CEG has alignment/support with Senior Management. One of the key ways we receive that alignment/support is through our monthly meeting with the Directors of the key divisions to discuss the key items of Energy in North America. Also key to success is celebrating the achievements of energy “wins” within the energy organization. As we look at the SEM Program participation, we consistently mention the energy efficiency rebates gained by the plants, but also promote the Energy Champions that take that “next step” to change the operational behaviors at the plant. As mentioned, benchmarking is key for energy management. Benchmarking occurs regularly from plant to plant, but Stellantis and the CEG also benchmarks externally with Energy Star and the Department of Energy – Better Building program. Benchmarking allows the CEG and Energy Champions to strive for operational excellence.
Knowledge
The last principle of the energy strategy is Knowledge. Knowledge is key to growing the expertise of the Energy Champions and further developing the complete energy organization. For knowledge we focus on the following items: Energy Workshops, Energy Champion Training, and Energy reporting using a variety of software platforms. In our participation with the SEM Program, not only have we grown the knowledge of the Energy Champions with regards to awareness and engagement, but the CEG has grown in knowledge as well. In addition, as a result of monitoring and tracking our energy savings as part of the SEM Program, we have increased our knowledge on pulling data from and using the various software platforms to report on such energy vectors as compressed air, chilled water, heating and ventilation systems, electrical consumption, and miscellaneous energy systems.
In summary, Stellantis in North America uses an energy strategy consisting of financial, technical, communication, and knowledge pillars to help manage energy consumption and drive change within the organization. The participation in the SEM Program has allowed Stellantis to drive improvement in all aspects of the energy strategy which has greatly contributed to the
success of the overall energy program.
Overview of the DTE SEM Program and Process
DTE Energy launched its SEM Program for large industrial companies in the DTE territory in Michigan in mid-year 2019. Stellantis operates several facilities in the DTE territory and initially subscribed the Jefferson North Assembly Plant (“JNAP”) and the Sterling Stamping Plant (“SSP”) for the SEM 24-month program period. Subsequently in September of 2020, the Sterling Heights Assembly Plant (“SHAP”), Mack Assembly Plant (“Mack”) and Warren Truck Assembly Plants (“WTAP”) also joined SEM for 24-month periods resulting in five (5) Stellantis facilities participating in the SEM Program.
The DTE SEM Program objective is to generate electricity and natural gas “operational” energy savings as distinct from other DTE Demand Side Management (“DSM”) programs that target energy consumption reductions from capital projects. Unlike DSM programs focused on capital projects where the implementation and/or modification of “technologies” results in energy savings, in SEM, the technology driving energy savings is the “human organization” combined with “data and information” on “energy consuming systems”. This activity can be referred to as “data driven energy management”.
The DTE SEM Program implementer is Leidos in combination with Energy Performance Services (“EPS”). Leidos carries out all program management work including interface with the DTE Program Administrator, submission of M&V reports, interface with the SEM program evaluator as well as administration of the incentives and payments to participants. Leidos also provides SEM services for DTE with hospitals and medium sized industrial facilities. EPS focuses on working directly with SEM Program large industrial participants and leads them through a series of activities aimed at generating “operational” energy savings that can be claimed by DTE for the SEM Program. The following consists of a brief overview of the activities that EPS takes participants through in the SEM Program.
Establishing Roles
A roles and responsibilities (R&R) matrix is defined for each participant to clarify the key participant organizational levels involved in SEM. Key roles that need to be fulfilled for the SEM participant are: (a) Executive Sponsor; (b) Plant Manager; (c) Energy Champion and (d) Energy Team. In the case of Stellantis, the Corporate Energy Group acts as the Executive Sponsor. The SEM implementor provides an SEM coach and SEM project engineer who run the weekly meetings, provide training, drive towards operational energy savings opportunities, prepare M&V savings reports for implemented operational actions and carry out background work to support progress. Other EPS staff support analysis activities, drafting of M&V reports, design and delivery of employee engagement activities and development and support for strategies for improving availability of energy management information.
Weekly One-Hour Meetings
Weekly one-hour meetings are scheduled on a recurring basis to provide a foundation for interaction between the SEM implementor and the SEM participant to keep the SEM Program and its activities in focus and part of a systematic routine.
Building an Energy Map
One of the first key tasks in SEM is to develop an understanding of how much energy is being consumed by the participating facility and to quantify what the actual main uses for that energy are. All industrial facilities have main utility meters for electricity and natural gas (or other fuels) from the energy suppliers however there is often a lack of energy sub-metering in the facilities to enable an accurate end-use quantification of energy. The work therefore is to estimate energy consumption using available energy sub-metering in combination with equipment nameplate information with estimated load factors and run hours to build an approximate end use breakdown of energy uses. This enables the production of an energy end use pareto that then serves as a springboard for selecting priority energy end uses for “treasure hunting” to find opportunities. Part of the energy mapping process also involves gaining an understanding of the various sources of energy information available and being used by the organization for energy management purposes.
Treasure Hunting
Treasure hunts can be carried out in many forms; however, the essential feature involves engaging the participant to find “actionable” opportunities that can be put into an action plan.
Treasure hunting for the DTE SEM Program is focused on finding operational energy savings that can be implemented in relatively short timeframes to create energy savings without requiring capital expenditure. Normally treasure hunting can be undertaken onsite however given the fact of COVID-19, EPS leveraged existing IT and control systems information to conduct “Virtual Treasure Hunts”.
Energy Management Information Sources
The sources of energy management information available at the Stellantis facilities related to significant energy uses are defined in Figure 1.
Significant energy uses. Significant energy uses include compressed air, chillers, lighting, HVAC, Process Energy, boilers and production systems.
Energy management information. Energy management information can be obtained via the following systems:
- BayWatch/BayView: a network-based compressed air management system (monitoring, control, analysis, integration, and automation) developed by Bay Controls. • TEKWorx: an optimization solution for boiler and chilled water systems capable of monitoring and controlling the pumps, boilers, chillers and cooling towers throughout a facility.
- Leidos Energy Management System (EMS): a flexible, web-based energy management suite that integrates energy metering, monitoring and control into a single streamlined solution. The use cases of this system are unique to each Stellantis plant, and typically include management of energy metering and monitoring/control of lighting, HVAC and other significant energy uses.
- DTE Loadwatch: an internet-based energy monitoring service that provides real-time, and historical, energy usage and demand data of a facility. This service can also be used to monitor and control stand-by generators to assure reliability.
- Real-Time Energy Management System (RTEMS): an energy monitoring system that compares real-time energy consumption to expected energy consumption to identify energy losses throughout the facility.
- Factory Information System (FIS): a system developed by Stellantis for monitoring and analyzing production levels throughout the facility
- Automatic Line Stop (ALS): a system developed by Stellantis for controlling automatic setback of energy intensive processes (i.e., ovens, fans, etc.), lighting, and HVAC during part or non-production periods.
- GE Daintree: a web-based solution with advanced lighting control and building automation capabilities
- Utility Billing Dashboard: a billing management system capable of automating and auditing payment of utility bills.
o The operational control table was innovated by EPS early in the pandemic in order to define target values for where significant energy use systems should be at in a non-production state and who is responsible for operating at those target values.
o The organizational elements involved in the management and control of energy under SEM include:
- Action plan implementation: As specific items are identified through the Treasure Hunting Process, they are transferred into the Energy Action Plan and progress in implementing these activities are tracked in weekly meetings.
- Energy Management Information System (EMIS) development: Due to the core nature of “energy management information” in SEM, the SEM Implementor delivers a specific workshop to bring into focus sources, systems and forms of energy management information within the facility as well as desired enhancements to better support strong energy management practices.
Measurement & verification (M&V) of energy savings: As specific operational energy savings actions are implemented; M&V reports are then produced by the SEM Implementor which are eventually claimed by the DTE Program. The DTE SEM Program Evaluator may select certain of these M&V Reports for detailed review.
- Employee engagement: Part of the SEM Program also focuses on development and implementation of an employee engagement process to engage employees in awareness of energy use, waste and actions that can be taken to drive energy waste out of the facility. The SEM Implementor delivers an energy employee engagement planning workshop culminating in the production of an employee engagement plan. Typically, employees in automotive factories (outside of the Energy team) have low to no visibility on energy consumption and costs within the facility as the key focus is on production. For SEM to be successful, engagement of employees in energy awareness is important for both broadening the source of energy waste observations as well as to sustain energy control actions over long time periods.
- Management Reviews: It is a key part of SEM to engage and leverage support from the Plant Managers of SEM Participants. The SEM Implementor organizes bi-annual Management Reviews with the Energy Team and Plant Manager to review progress, results and issues that may require support from the Plant Manager.
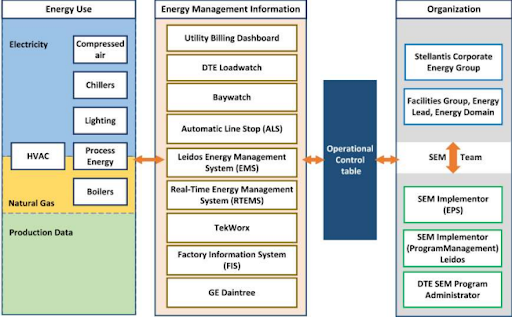
Stellantis Perspective
Along with many other industries, the automotive industry was greatly affected by the COVID-19 virus. In 2019, the virus forced many Stellantis plants to cease production for almost two (2) months. The sudden shift in operation left our energy organization and the operations team to quickly pivot to “full shutdown” mode instead of the typical maximum production mode. Prior to the virus and the global pandemic, Stellantis engaged with DTE Energy and EPS to participate in the SEM Program. The team started to engage in January of 2020 and started down the “typical” SEM path. As the world began to shift to the global pandemic world, the entire group gathered to understand how we could together change the operational behaviors at the plants participating in the SEM Program to minimize energy consumption and drive shutdown curtailment.
After spending the initial meetings to introduce the plant operations and equipment, the working group for the SEM Program quickly shifted the attention to how the plant operates during shutdown periods and how to maximize operational efficiency. Working together the team was able to quickly identify previous best performance in terms of electrical and natural gas consumption. Using that target as a guideline, the team worked together to minimize the consumption of various energy systems.
The simple approach of using an Operational Control Table was developed. While the plant knew what equipment to shut down during idle periods, there was nothing documented to say what the criteria was or who was responsible for the operation. The Operation Control Table focuses on the key items: System, Criteria/Indicators, Units, Operation Mode Targets, Network System, and Responsible. An example skeleton of this is found on the next page.
Together as a SEM group we identified the major energy systems, such as: Compressed Air, HVAC, Weld Water, Building Lighting, Chilled Water, Compressed Air, etc. After identifying the energy systems, we then developed a comprehensive list of criteria and indicators to be used per system to understand what are the main drivers behind energy consumption. A good example of criteria/indicators for Compressed Air for example might be: pressure setpoint (PSI), cooling water (temperature), compressor operation (# of compressor running), efficiency (cfm/kW), Flow (cfm), and power (kW). These indicators or KPI’s help us to understand how we should be running the system in different modes. Next, the group examined the different modes that are present in the plant, for example: Production, Non-Production (1 day), Non-Production (> 1 day), Demand Response Mode, etc. After identifying the different operating modes, we then set out to list the ideal running criteria for those different modes. For example, one might reduce the number of HVAC units running from Production to Non-Production due to the air change requirements. Also, the group focused on where this data is available and how is it controlled. In Manufacturing facilities, it’s not uncommon to have several different software systems used to control the energy systems. In many cases there might be a different system to operate the HVAC, to operate the compressors, and to operate the chilled water systems. Lastly, and probably one of the most important steps, is to assign responsibility for who is ultimately responsible for putting the equipment into the proper operation mode setpoint. This is often the weakest link in the plants, pinning down the operation responsibility to one or a group of people to properly control the systems. In many cases it’s preferred that the equipment operates on an automatic schedule, but still human intervention is always required to ensure success.
This very simple table allowed Stellantis to achieve historical shutdowns during the COVID-19 shutdown period, surpassing the results from other shutdowns or holiday periods. As
an organization, we have found success by documenting the procedures and also following up and auditing those procedures. In this case, this is no different. The Operational Table provides a documented approach for achieving curtailment success and it allows the Facility Managers or Energy Champions at the site to continually judge success depending on the operation mode in place.
Table 1. Stellantis Operational Table
System | Criteria / Indicators | Units | Target value in idle mode | Responsible |
Chillers | Supply Temp Set-point, % Loading | °F | ||
HVAC (Air
Houses) |
Set-point temp
(Manufacturing, offices) AHU fans & aux. equipment |
°F | ||
Compressed air | Pressure Set Point, Efficiency, Flow, Power | psi | ||
Weld water | Pump ON/OFF, Temp Set point | # Units | ||
Lighting | Bodyshop, Paint, Assembly | ON/OFF | ||
Process | Paint shop, RTO, HVAC | On/Off |
Source: Leidos-EPS, DTE SEM Program 2020.
As the CEG, one of our top missions is to spread Best Practices and share success stories with other plants. This is no different. Once we saw the success and the dramatic decrease in energy consumption, we shared this Operational Table approach with the other Manufacturing plant in North America and globally. The other plants have now documented their operation modes and criteria and as a region we are seeing improved non-production curtailment performance. The performance from the facilities that achieved “historic” results were celebrated by our Senior Management, being labelled as “Energy Warriors” by the Vice President of North American Manufacturing. These achievements were excellent and were celebrated by all around the organization.
As we continue working with the SEM team, we are excited not only to increase the energy awareness at our facilities, but also to train additional Stellantis team members, some of which are on the floor, to attack energy consumption and improve operational behavior where possible. The program has re-energized the energy community within Stellantis and has allowed the energy organization to have a greater reach.
In reviewing the SEM Program with DTE Energy and EPS, this program has been quite a strength for our energy organization and allowed us to not only obtain incentives for historic energy performance, but also reduce our total consumption. This improvement helped our “bottom line” at Stellantis and allowed us to reach our energy targets and KPI’s for the year.
SEM Implementor Perspective
Stellantis already had a structured energy management process in place when they joined SEM however as with all continuous improvement processes, they can always be strengthened. As the DTE SEM Program is only looking for “operational” energy savings and does not pursue capital projects for energy reduction (those are supported by other DTE energy efficiency programs), this singular focus on operational energy savings was the basis of the Stellantis participation in the SEM Program. When the first two (2) facilities (SSP and JNAP) joined the SEM Program the SEM Implementer proceeded in its planned way to gradually progress along the SEM pathway. However, when the COVID-19 pandemic hit with full force in early 2020 and the stamping and assembly plants of Stellantis were forced to stop production completely, the SEM Program was thrown a major curveball. We noticed however that the “idle” loads of the Stellantis plants at zero production were still quite significant despite there being some targets within Stellantis for non-production energy. Given the focus of SEM on generating operating energy savings, the idea of working with the plants to drive their zero production “idle” load down further was discussed. It was further discussed that if we could use this period to gain better control over idle energy when there was no production, that we could then leverage that energy management control to expand energy savings when the plants returned to normal operation.
The further challenge that was faced in trying to manage energy during COVID-19 was that there were very few people in the plants. We could see the overall plant energy consumption (gas and electricity) using remote connections to the utility meters, however we needed to drill deeper into the major energy consuming sub-systems to diagnose where they were in terms of energy consumption. The SEM joint team worked its way through each major energy using sub system such as compressed air, chillers, HVAC, boilers, lighting, and process systems to gain access to information concerning the idle condition of each of the systems. The SEM Team used specific information gateways to those systems which could be interrogated remotely and analyzed. An operational control table was constructed using a simple excel table to document each system and its sub-components and to define where it should be in terms of energy consumption or other criteria relative to the specific mode the plant was in. The modes were defined in terms of “non-production” greater than a specific amount, shorter than that amount as well as part production and full production. SEM therefore used the time of restricted COVID-19 to define the specific criteria for where systems and sub-systems should be in each of the modes. Gaining access to a full complete plant non-operating mode such as with COVID-19 presented an opportunity to challenge the organization to push the setbacks in “non-production” mode beyond their standard levels and thereby generate SEM savings and set up future best practice values for energy setbacks. Working with a mature organization such as Stellantis, coupled with availability of digital information on significant energy uses enabled the SEM team to drive energy management deeper.
The efforts to use the negative situation of COVID-19 to creatively mine out energy waste from the participating Stellantis facilities yielded substantial energy savings results which were valued by Stellantis as well as by the DTE SEM Program. From the platform of using this difficult period to gain better energy management control, the SEM team gained valuable knowledge and has continued to leverage this approach as plants have returned to operational modes.